|
ISOWALL Insulating Panels
.
ISOWALL Panels meet your size and insulation
requirement.
|
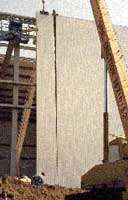
From large distribution warehouses
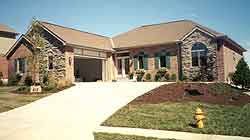
To a new home...
|
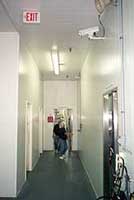
To multiple room processing plants
|
ISOWALL brand insulating panels are stressed skin sandwich panels consisting of steel, aluminum, or composite facings permanently bonded to a plastic foam core with a heat polymerizing adhesive. The panels are produced on a continuous, integrated production line which performs roll forming, core shaping, laminating, and sizing functions. This state of the art line, developed by
AIC, insures a high standard of appearance and quality.
FEATURES and BENEFITS |
-
Fast, Easy Installation
-
Easy to Clean
|
-
USDA Accepted
-
Strong Technical Support
|
APPLICATIONS |
- Holding
Freezers
- Test
Rooms
- Holding
Coolers
- Clean
Rooms
- Food
Processing
|
- Cold
Docks
- Blast
Freezers
- Portable
Buildings
- Blast
Chill Rooms
- Ripening
Rooms and CA Storage
|
..
|
.
GENERAL SPECIFICATIONS
GENERAL SPECIFICATIONS ISOWALL™ BRAND ISULATING PANELS
1.0 Insulating panels as shown on the drawings
shall be ISOWALL brand insulating panels as manufactured by Advanced Insulation
Concepts, Inc., Florence, Kentucky.
1.1 Panel facings shall be
permanently bonded to the insulating core with a heat polymerizing adhesive.
1.1.1 Exterior facings shall be .020" or .024"
galvanized steel, G-90 Hot dipped, conforming to ASTM A653 Grade 33, precoated with a nominal 1 mil thick silicone modified polyester finish (Beige,
Limestone or Polar White). Facings shall be designated as smooth or stucco embossed.
1.1.2 Interior facings shall be .020" or .024" galvanized steel, G-90 Hot
dipped, conforming to ASTM A653 Grade 33, precoated with a nominal 1 mil thick Polar White silicone modified polyester finish acceptable to the USDA. Facings shall be designated as smooth or stucco embossed.
1.1.3 Stainless steel interior facings, where designated, shall be .018"
minimum Type 302B stainless steel, stucco embossed.
1.1.4 Plastic Coated Steel interior facings, where designated, shall be
.020" galvanized steel, G-90 Hot dipped, conforming to ASTM 653 Grade 33 precoated with .004" White polyvinyl chloride Plastisol
acceptable to the USDA. Facings shall be designated as smooth or stucco embossed.
1.1.5 Composite facings, where designated, shall be .060" fiber-glass
reinforced polyester, conforming to NFPA Class C or better, laminated to 5/8"
oriented strand/aspen flake board.
1.2 Panel edges shall be precisely formed to assure foam to foam contact and
alignment of panel facings and to facilitate vapor barrier and sanitary sealing as required.
1.2.1 Tongue and Groove Edge Treatment
(TAGET) shall be continuously roll formed into facings such that the formed tongue of one panel fits into
the groove formed by the facing and core of the adjacent panel. In addition, the core shall be grooved to accept a .25" x 2.75" tempered
hardboard alignment spline.
1.2.2 Panels shall be formed and grooved to accept aluminum or poly
chloride H-Moldings. In addition, the core shall be grooved to accept
a .25" x 2.75" tempered hardboard alignment spline.
1.3 Metal panel facings shall have a roll formed configuration which enhances
appearance and panel strength.
1.3.1 Exterior wall facings with TAGET shall have a continuously roll
formed rib/groove configuration consisting of 1.375" x 0.10" ribs
alternating with 0.06" deep grooves spaced so that the joint between panels simulates
a groove.
1.3.2 Interior facings with TAGET shall have a continuously roll formed configuration consisting of 0.06" deep grooves spaced approximately 6" apart so that the joint between panels simulates a groove.
1.3.3 Both exterior and interior metal facings with H-Moldings shall
have a continuously roll formed configuration consisting of 0.04" x
0.75" shadowlines spaced 5" apart.
1.4 Insulating core thickness and type shall be determined based on the temperature
differential and other building requirements.
1.4.1 Expanded Polystyrene shall have the following properties:
DENSITY (pcf) 1.0
ELASTIC MODULUS (psi) 200
SHEAR MODULUS (psi) 300
K-FACTOR AT 40 F MEAN .24
1.4.2 Extruded Polystyrene shall be designated Styrofoam™ Blueboard or equal and shall conform to product specifications published by the manufacturer.
1.4.3 Polyisocyanurate foam shall be designated Elfoam™ T200 or approved equal and shall conform to product specifications published by the
manufacturer.
1.4.4 Core materials shall be tested by an approved laboratory in accordance with ASTM E84 and have a flamespread rating of 25 or less and a smoke developed rating of 450 or less at a thickness of 4 inches.
CAUTION: Plastic facing and
insulating core materials are combustible
and may present a serious fire hazard if improperly used or stored. Their flamability
characteristics are defined for purposes of comparison with other materials by various standard tests such as ASTM E84. However, such tests do not measure the performance or reflect hazards presented by these materials or any other materials under actual fire conditions.
1.5 Dimensions
1.5.1 Panel width shall be 47.375 inches +/- 1/16 inch.
1.5.2 Panel thickness shall be as ordered +/- 1/16 inch.
1.5.3 Panel length shall be full height unless otherwise designated. Length tolerance shall be +/- 1/8 inch.
1.5.4 Panels shall be fabricated in the field to fit the structure including sloping walls to fit roof shape and fitting wall corners.
2.0 PANEL ACCESSORIES
2.1 Aluminum Extrusions shall be 6063 alloy.
2.1.1 Exterior painted aluminum extrusions shall color match the panels and be coated with a nominal 1.0 mil polyester finish.
2.1.2 Anodized aluminum extrusions shall conform to Architectural Class II (AA-C22-A31).
2.1.3 Interior painted aluminum extrusions shall color match the panels and be coated with a nominal 1.0 polyester paint acceptable to the USDA.
2.2 Polyvinyl chloride H-Moldings and other trim shall be manufactured with virgin PVC, color to match
FRP, and be acceptable to the USDA.
2.3 Hardboard splines shall be ¼" x 2 - 3/4" x 96" tempered hardboard.
2.4 Trim around doors and other penetrations shall be fabricated by installer using materials which match the panel facing.
3.0 WARRANTY
3.1 ALL ISOWALL panels furnished by Advanced Insulation Concepts, Inc. shall
conform to the specifications set forth above and in the Bill of Materials used to order them and will be free from defects in material and workmanship when delivered to the job site. If any of the panels fails to conform to the
above warranty, AIC will, upon written notice thereof received within one year following the initial date of installation, repair or replace, at AIC's option, the
nonconforming panels. This Warranty shall not apply to failure caused by acts of God, fire, abuse or abnormal use, or other casualties, not to panels which
have not been used in building application of adequate design, engineering and
construction and in accordance with AIC's current design and
installation recommendation.
AIC MAKES NOT OTHER WARRANTIES, EXPRESS OR
IMPLIED (INCLUDING WITHOUT LIMITATION, MERCHANTABILITY, FITNESS FOR A
PARTICULAR PURPOSE, OR AGAINST INFRINGEMENT OF ANY PATENT). REPAIR OR REPLACEMENT, AS SET FORTH HEREIN, IS THE SOLE AND EXCLUSIVE REMEDY OF PURCHASER AND WILL SATISFY ALL LIABILITIES FO AIC TO PURCHASER WHETHER BASED ON CONTRACT,
NEGLIGENCE OR OTHERWISE ARISING OUT OF THE PURCHASE OR USE OF THE PANELS. IN NO EVENT WILL AIC BE LIABLE FOR INCIDENTAL
CONSEQUENTIAL DAMAGES.
3.2 Long term written warranties on exterior paint finishes are available. Contact AIC for additional information.
.
|
|
|